There’s no doubt that outdoor electronics is big business. According to a recent study by Fortune Market Insights, the global market for outdoor power tools was expected to be worth $33.5 billion in 2023, and could reach nearly to $50 billion by the end of the decade. A similar survey by Future Market Insights of the global outdoor lighting market put its value at nearly $13 billion in 2023.
With such sizable revenues at stake, it is vital that outdoor electronics are thoroughly tested to ensure they will perform successfully over their life cycle. The first stage of designing a test protocol for outdoor electronics is to define the product’s “end-use environment,” says Dr Florian Feil, senior consultant for weathering technology at the test equipment maker Atlas Material Testing.
Feil says: “So is the product permanently stored outdoors? Or is it mainly stored indoors and maybe only on dry days taken outside? Because a product which is commonly kept outdoors will be tested differently from one that is kept inside.”
Naturally, the biggest factor differentiating the testing of outdoor electronics from those designed for indoor use is the effect of weather. In general, the requirements of outdoor applications are more severe, with outdoor electronics needing to withstand the effects of rain, wind, sunlight, and humidity.
Sun, rain and heat
Of these environmental factors, the one that has the biggest weathering impact on the product is sunlight, says Feil.
“The core environmental stress in weathering is solar radiation,” says Feil. “It is the most critical to initiate degradation processes in polymers and coatings. The degradation processes also depend very much on the spectrum of the light source. Therefore a realistic simulation of solar radiation is the key to simulate outdoor weathering realistically.”
The effects of heat and rain are also important, he says.
Feil says: “Heat accelerates degradation processes, but also depends on the environment and the solar absorption. Darker surfaces get hotter compared to lighter, this also needs to be considered.
“Water, as relative humidity, but also in liquid form as rain or dew is also important. Coatings or combinations of different materials in an electronic product are sensitive to the cyclic stress of water uptake and release, which might cause stresses due to different swelling behavior.”
Weathering testing of outdoor products therefore involves simulating these environmental factors, says Feil.
He says: “Weathering testing is basically a simulation (maybe intensified) of the environmental stresses. We often talk about the black box approach. We simulate the weather, which has basically the same effect on all materials.”
Leaking testing
Testing the effect of water is especially important for electronics products. Most electronics will malfunction if they are exposed too much humidity so “the requirements typically for components that are used outdoors is that they’re completely sealed,” says Gordon Splete, product manager at leak testing experts Cincinnati Test Systems.
To test the effectiveness of the seals the electronic component is put inside a chamber and pressurized from the outside. “We then measure for pressure loss into the part correlated to a non-liquid leak rate,” says Splete.
According to Splete, pressurized air is generally preferred over water because it has much greater sensitivity than water.
For example, in the case of extremely small hole sizes water will actually plug the hole while air will continue to flow through it.
The instrumentation used to measure leakage is known as pressure decay technology, and it is used to record pressure loss over time. According to Splete, the technology is capable of calibrating for changes in atmospheric pressure, meaning that it can compensate for differences in atmospheric pressure if the testing is done in different parts of the world.
The type of test set-ups used to simulate outdoor environments in the lab depend to some degree on the budget of the client, says Feil, but the gold standard for simulating sunlight is the xenon arc lamp, a specialized type of gas discharge lamp that produces light by passing electricity through ionized xenon gas at high pressure.
In order for the material testing to imitate as closely as possible the real-world environment, it is important to test all the environmental factors at the same time. For this reason xenon arc lamps are usually integrated into test chambers that can also simulate heat and humidity.
Stress testing vs weathering testing
Broadly speaking, the material testing carried out on outdoor electronics can divided into two categories: stress testing and weathering testing.
It is important not to confuse the two, says Feil. “Weathering testing must be considered as an aging test, but not as a stress test, which is also common for component testing. [For weathering testing] we look at slow aging processes, which continuously affect the performance of the product. Typically, weathering does not cause a dramatic failure of an electronic device.”
While weathering testing assesses the slow impact of environmental stresses on a product over time, manufacturers cannot wait the entire life cycle of a product to understand what this impact will be.
As Michel Comtois, president of Micom Laboratory, an environmental testing company based in Montreal, puts it: “If you want to warranty your iPhone for corrosion for five years, for instance, you don’t want to have to wait for four years, 364 days, 24 hours, 59 minutes, 59 seconds of testing to say, ‘Yeah, my phone is okay.’”
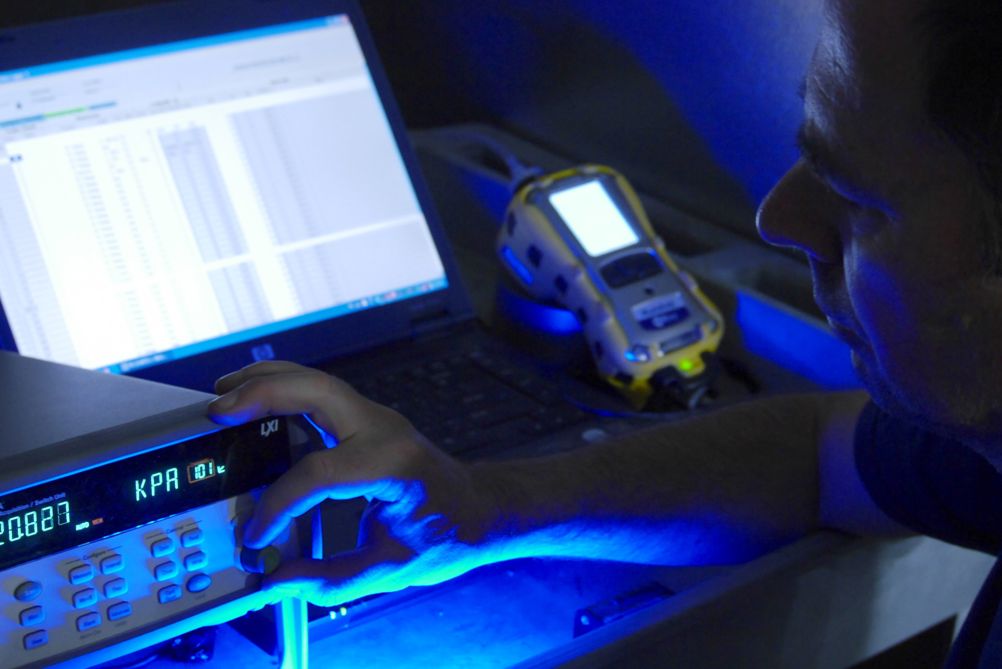
Accelerated aging
To speed up the process, materials testers use a process known as accelerated aging. This process is based on the 10-degree rule, which stipulates that for every 10-degree increase in temperature the reaction rate of the material is doubled.
However, Feil says that the aging effect is highly dependent on the sensitivity of the material being tested. “It’s very specific to the material,” says Feil. “There are chemical processes which are very temperature-dependent, and the temperature effect is different from material to material. So there is no general rule.”
That said, Feil offers as a “ballpark figure” that a year of product’s life cycle could be condensed into 1,000 hours of accelerated weathering testing. However, without a precise understanding of the variables, accelerated weathering testing can give an unrealistic picture of natural aging, says Feil.
“We can increase the irradiance above the natural limit to get faster aging but it’s something you have to be a bit careful with,” he says. Some artificial light sources, says Feil, beam out UV radiation “beyond the natural UV levels and are very aggressive, causing very drastic degradation, which is typically not realistic.”
It is therefore important to compliment the accelerated weathering with a control. For this reason, Atlas has outdoor test sites in Florida and Phoenix and other places around the world where material testing is conducted in real-time in the natural environment “because it’s the most realistic way to test.”
Material vs product testing
Most weathering testing is carried out at the materials level first.
Weathering testing of components or entire products is rarer, in part because of the expense involved. Micom Laboratory, for example, has a walk-in environmental test chamber big enough that “we could literally drive in an all-terrain vehicle,” says Comtois.
But he adds: “Obviously, the larger the chamber the more expensive it gets for us to run, so the more expensive are the acquisition costs and the cost of testing.”
Chamber size also limits the type of testing that can be done, Comtois says. “In our shop we have nine climatic chambers,” says Comtois. “Some of them will be smaller but will have a very rapid cooling rate or heating rate.
The larger chambers usually will not have cooling rates as fast, and depending on the test requirements we’re going to be limited by the chamber size we can use if we want to respect the cooling rate that is required for the test.”
One of Micom’s environmental test chambers is for thermal shock testing and is capable of alternating between lows of -68C and highs of 200C in repeated cycles.
Thermal cycling like this can be used to replicate the effects of the dayand night-time temperature differentials experienced by an electronic – for example, a lawnmower – stored outdoors.
These temperature changes, particularly if the night-time temperature regularly drops to below freezing, can lead to problems over time like condensation forming inside the product’s components, says Feil.
The effects of thermal cycling can even lead to problems in indoor electronics, says Comtois. When you turn on your laptop it causes thermal expansion, and when you turn it off, it shrinks back,” says Comtois. “It’s microscopic but you do that a thousand times you might get some circuits that start breaking down.”
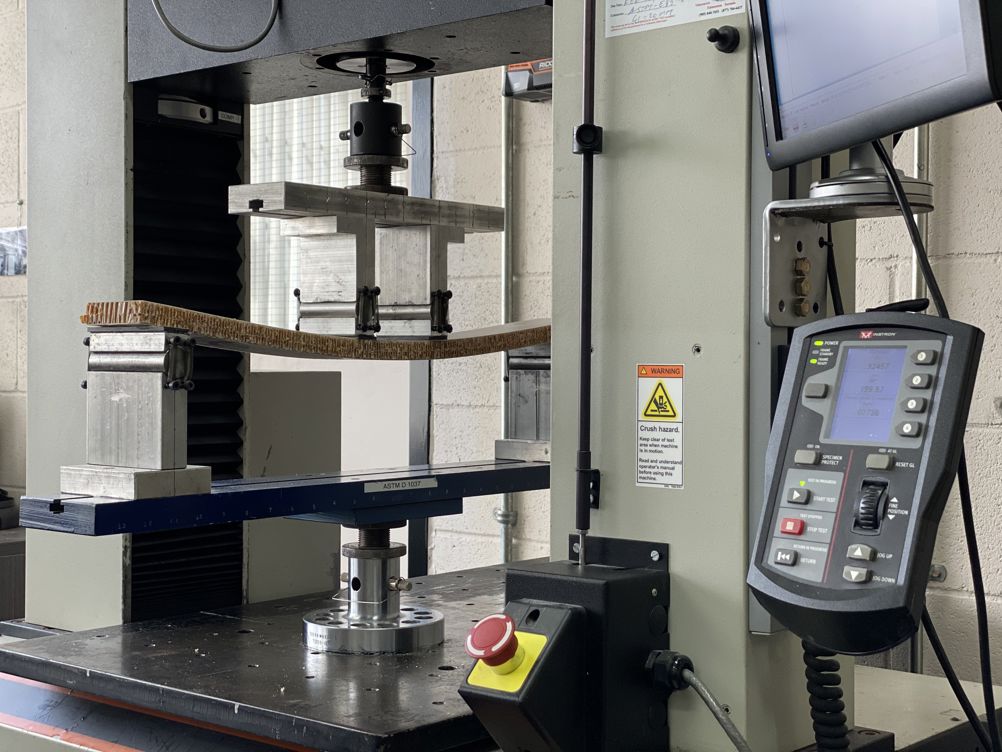
Secondary factors
While most weathering testing focuses on the cumulative effects of sunlight, humidity and temperature, many outdoor electronics have very specific uses cases that expose them to other environmental factors. A lawnmower, for example, is constantly exposed to grass and soil, a chainsaw to wood and sawdust.
According to Feil, these “secondary stress factors” are kept out of weathering tests in part because it would complicate the test set-up too much and in part because traditional weathering testing equipment is not designed to simulate these factors.
They are therefore tested separately. A common example of this secondary testing, says Feil, are abrasion tests carried out using artificial turf, in which the turf is mechanically rubbed against the material or product to see how much it degrades it. CET&D
This article first appeared in the March 2024 issue of Consumer Electronics Test & Development magazine. To read the full issue, click here.